Consultancy in RCM Development
We render consultancy services in 'RCM development' at your company.
Don't you think -
That your Plant & Machinery should give you flawless services throughout their lifetime?
That there shouldn't be any sudden failure of the important machine?
That there should be zero production losses? Does reduced maintenance cost?
Reduced Tension on Maintenance Team? No Fatal Accidents in a company?
The one-word solution is 'RCM' - The Reliability Centered Maintenance of the entire plant.
What is Reliability Centered Maintenance?
Don't you think -
That your Plant & Machinery should give you flawless services throughout their lifetime?
That there shouldn't be any sudden failure of the important machine?
That there should be zero production losses? Does reduced maintenance cost?
Reduced Tension on Maintenance Team? No Fatal Accidents in a company?
The one-word solution is 'RCM' - The Reliability Centered Maintenance of the entire plant.
What is Reliability Centered Maintenance?
As the name suggests, it is maintenance practices keeping RELIABILITY at centre
or focusing on reliability.
RCM is based on FMEA/ FMECA of listed assets and PdM depends on the criticality of equipment.
FMEA - Failure Modes & Effect Analysis
FMECA - Failure Modes, Effects & Criticality Analysis
Now, we will start with the P-F curve and step-by-step we will reach RCM. You are
very much aware of the P-F curve. This potential failure - functional failure curve is based on Predictive Maintenance. And as PdM is part of RCM we should study
it here.
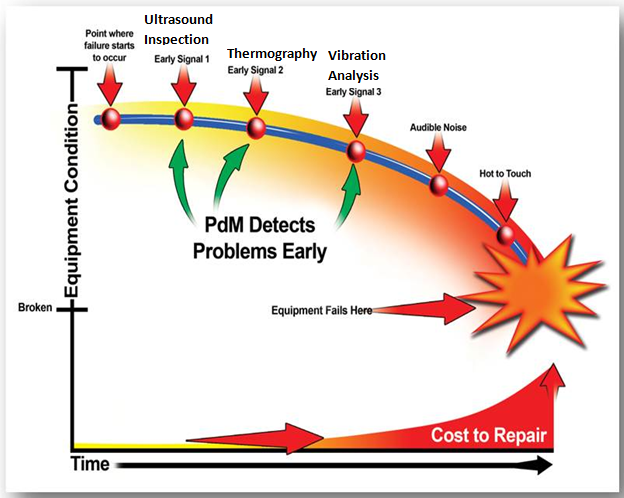
or focusing on reliability.
RCM is based on FMEA/ FMECA of listed assets and PdM depends on the criticality of equipment.
FMEA - Failure Modes & Effect Analysis
FMECA - Failure Modes, Effects & Criticality Analysis
Now, we will start with the P-F curve and step-by-step we will reach RCM. You are
very much aware of the P-F curve. This potential failure - functional failure curve is based on Predictive Maintenance. And as PdM is part of RCM we should study
it here.
The P-F curve explains a part of RCM and that is optimized maintenance during normal life zone or useful life zone (Constant Failure rate portion of Bathtub Curve). Hence, while
thinking RCM we should see beyond useful life zone i.e., beyond the P-F Curve.
The reliability of any machine starts from the design of that machine then manufacturing
quality and installation of that machine. This part comes before the P-F Curve. This is early life zone of bathtub Curve and even the period before this zone.
After the P-F curve part is 'Wear out or Ageing' part of the bathtub curve. There is nothing much that we can do in this zone, then replacement of parts or machine itself.
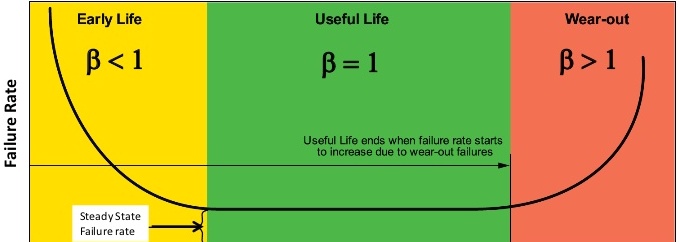
We have reconciled P-F Curve, Bathtub Curve and Methods of Maintenance and invented
a new module of Reliability Centered Maintenance.
We have to start our RCM program right from Procurement stage of our assets. The asset
should be suitable for our operating conditions, suitable for preventive maintenance, and
suitable for Predictive Maintenance.
The installation of machines should be cross-checked for any deficiencies and flaws in
the machine assembly, foundation quality, base rail etc. 'Burn In' practices also supports
in confirmation of the quality of manufacturing and installation quality. The 'Burn In' also,
helps in correcting our operating quality.
We worked on this concept and extended our services for maintenance part during normal
life zone or useful life zone of the bathtub curve. This part of maintenance includes Breakdown
Maintenance and Predictive Maintenance. Let us explore Breakdown Maintenance &
Preventive Maintenance.
Breakdown Maintenance explained below,
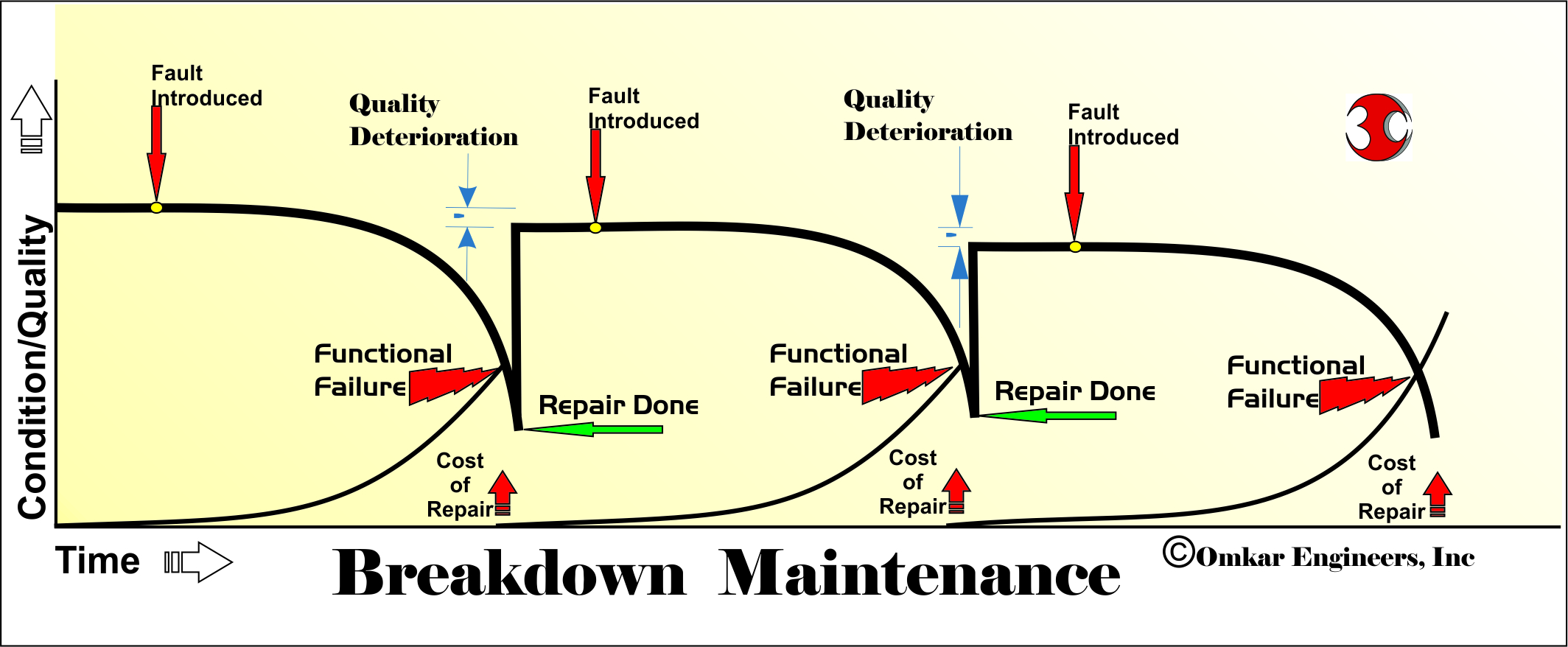
While considering machines (machine parts) under breakdown maintenance, we should
remember that, the quality & efficiency of repaired machine deteriorates after every repair.
Predictive Maintenance explained below,
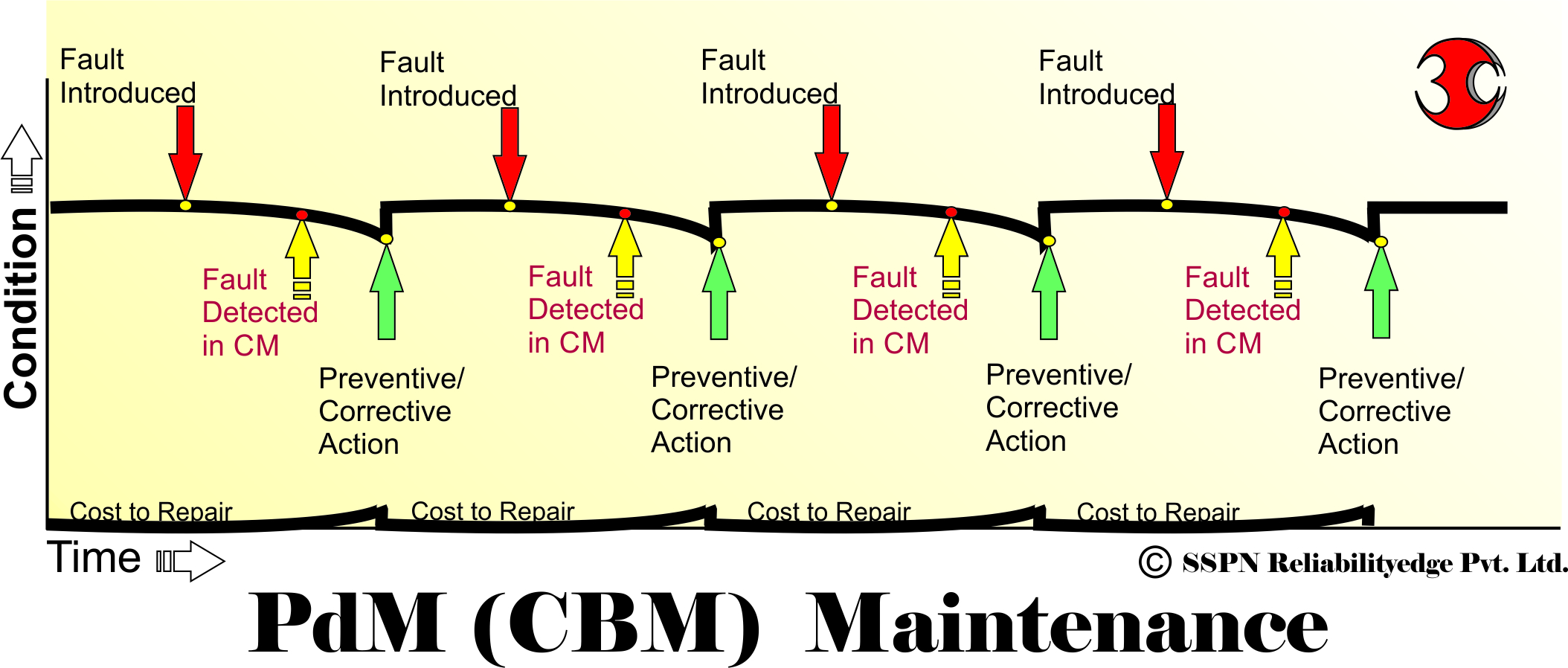
In case of properly implemented predictive maintenance, the quality and efficiency of
the machine hardly deteriorate. Also, the cost of rectification remains negligible compared
to breakdown maintenance.